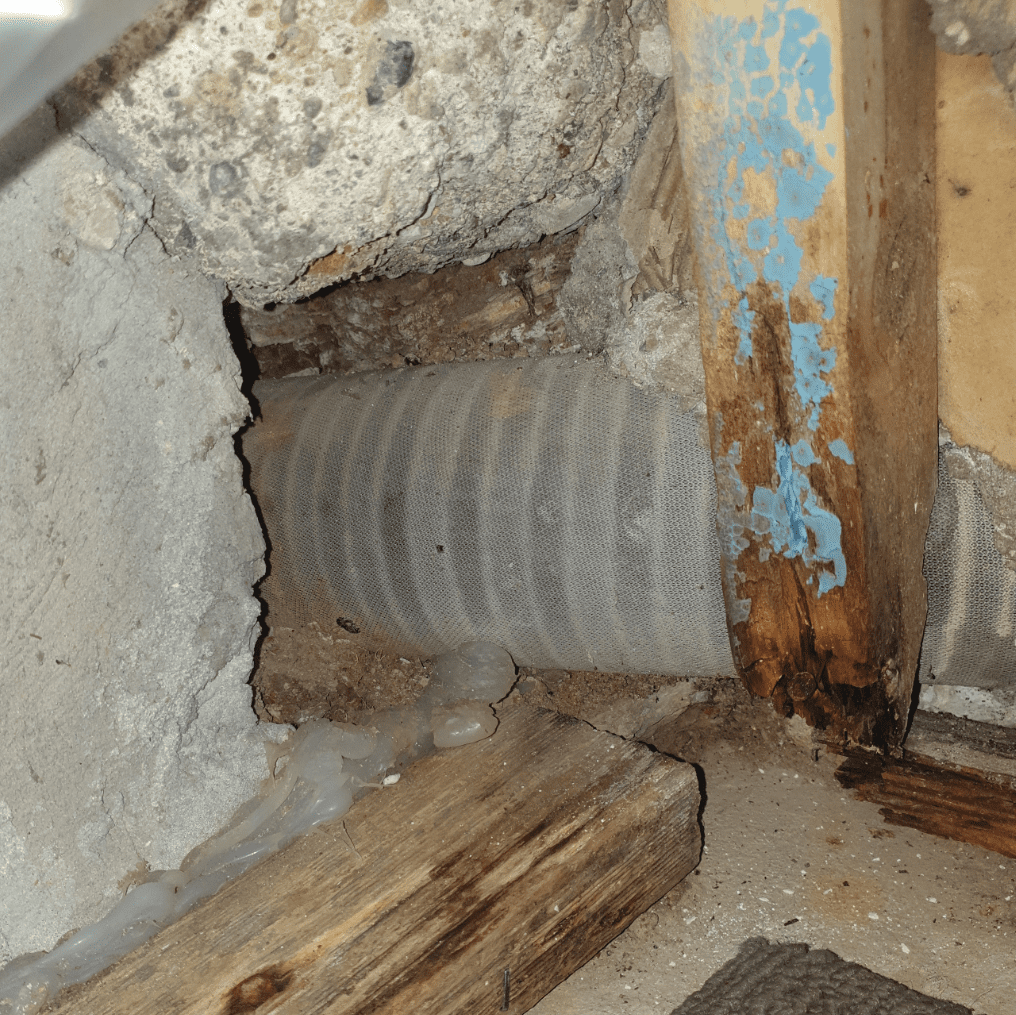
19 Jan Hillside basement water ingress solution
Subscribe to our newsletter
Remedial waterproofing of basement storeroom area
The part of the building that was affected by water ingress is partially built underground in a hilly area of Brisbane and was originally a garage that has since been converted into a storage room with adjoining bedrooms.
Buildings that are cut into a hillside stand a greater risk of having the hillside affected by natural water pathways, saturated soil, elevated water table and hydrostatic pressure during prolonged or heavy rain events. It is important that there are adequate drainage systems in place to direct water away from basements walls and foundations to eliminate water build-up around the building. If water is allowed to pool, it is just a matter of time before water finds its way in through joints and cracks in the concrete or masonry.
A previous contractor had attempted to provide a solution to drain the water that was building up underneath the house by installing an Ag pipe in a boxed-in area under the house. The Ag line runs through the corner of one of the bedrooms and this created a new problem because water from under the house ended up being fed into the bedroom via the Ag pipe and consequently flooded the room.
Only solid pipes should be installed under the building to ensure that water is not introduced under your house through the perforations in the Ag pipes. Ag pipes should not be installed UNDER or INSIDE your house.
If there was absolutely no possible way of redirecting the water with an Ag line around the building, then a solid PVC pipe should have been used in the section that is inside the house.
Image: The pipe you can see in this photo is an ag pipe that runs through the corner of one of the bedrooms. A slotted/perforated PVC pipe is designed to sit in the soil and redirect water to improve the subsoil drainage. Ag pipes should not be installed under or inside your house.
The remedial solution to the affected areas in the basement:
- Plumber to install a correct drainage system
- Leak sealing injection and installation of reverse side membrane
A reputable plumber rectified the issue by providing an appropriate solution to redirect water that builds up under the house. Once the plumber had completed his work and the new concrete in the corner had cured, Waterstop Solutions carried out leak sealing injections into the identified areas of water ingress followed by the application of two thick coats of cementitious negative side membrane (NSM) on top of a priming coat.
Leak sealing injection of floor/wall joint: Our leak sealing specialist intersected the joint at intervals and injected a flexible polyurethane at high pressure into the joint. After allowing the polyurethane to react and bind with any water present in the joint and surrounding concrete to form a flexible seal, the injection ports were removed, and holes filled with a suitable concrete repair material.
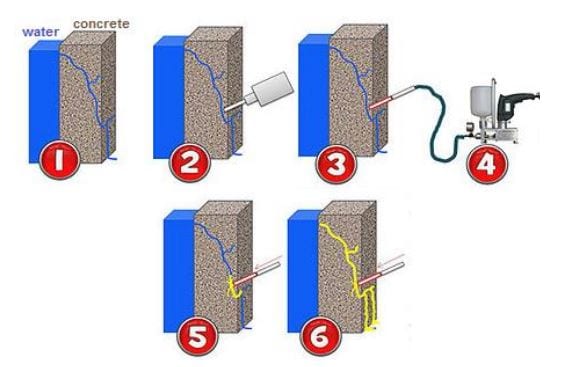
Polyurethane leak sealing injection into cracked concrete step by step.
The leak sealing process, or polyurethane injection, involves the high-pressure injection of flexible water-reactive polyurethane (resin) into targeted areas to form a durable seal. This system is ideal where a long-lasting waterproof seal is required to stop the passage of water or other liquids through gaps, cracks, joints, and penetrations – typically in concrete and masonry constructions.
It is a highly specialised process, requiring the skills of experienced operators. At Waterstop Solutions, our technicians perform polyurethane injection works frequently. They receive ongoing training from industry leaders which equips our technicians with expert skills and knowledge.
We use the best Polyurethane (PU) product available as our primary injection resin. This resin offers superior performance. Its main features include permanent flexibility; very low shrinkage; water potable; low viscosity; and a hydrophilic reaction – it is the same product that is pre-approved by major traffic authorities around the world for major infrastructure assets.
This system can be installed in any weather – in fact, the wetter the better, as it reacts with water right before your eyes. In dry weather, flooding the source of water entry (where possible) may have a similar effect.
Waterstop Solutions’ proprietary injection system exceeds the highest injection process and safety standards in Australia and internationally throughout Europe and the USA.
We continually review and reassess the method, always striving to hone and improve our systems. Our proprietary leak sealing system forms a long-lasting flexible seal against water ingress which also withstands normal building movement between construction elements and details.
Walls: After the leak sealing injection of the floor/wall joint was completed, a primer was applied to the wall before the reverse side cementitious waterproofing membrane (NSM100+) was installed in multiple layers.
Our waterproof membrane (NSM 100+) is a two-component acrylic modified cementitious coating that is flexible so that it can handle a small amount of movement.
This membrane is a hardwearing, seamless waterproofing membrane for effective concrete protection. It also provides an effective barrier to waterborne salts and atmospheric gases.
The NSM 100+ system is breathable. Whilst repelling water, it allows moisture to pass through it slowly as a vapour, allowing the substrate to breathe.
It is water-based, so any vapours are non-toxic and ideal for potable water usage and it can be painted over in water-based breathable paints (e.g. low sheen or matt acrylics) and most water-based after-trades such as direct stick, tiles or render.
Give us a call to discuss the best protective treatment application for your vertical and horizontal surfaces to help you choose the appropriate product and methods to protect them and how to best prepare the surface before installation for best performance.
If you have any issues with water ingress, rooftop leaks, leaking balcony, leaking basement, cracking concrete slabs, structural cracks, concrete deterioration, spalling concrete, concrete cancer, deteriorated joints, moisture, seepage, efflorescence, rising damp and/or high-flow active leaks in concrete structures, we would be happy to assist you. You are welcome to contact us with any questions that you may have.
Brisbane office: (07) 3205 1899
Email: [email protected]
Sydney office: (02) 9346 8308
Email: [email protected]
Are you interested in finding out more about the various remedial building services we are providing?
Please click on the image below to download Waterstop Solutions Capability Statement
Waterstop Solutions Capability Statement is now available to download as PDF. (The image is clickable and opens up a link to our Capability Statement).
Good maintenance begins with a proactive approach to maintain, keep, preserve and protect a building.
Remember that seepage/water ingress into areas such as balconies, basements, concrete roofs, car parks and retaining walls, should not be ignored – call a remedial waterproofing professional today for an assessment to provide you with the best solution for your situation.
At Waterstop Solutions, we carry out a wide range of remedial works to concrete structures post-construction stage in Brisbane, Gold Coast, Sunshine Coast, Sydney and outlying areas in Queensland and New South Wales.
Equipped with major civil works experience, we can quickly determine the best approach to rectify all seepage and concrete deterioration issues.
It takes licenced remedial waterproofer and leak sealing experts like us at Waterstop Solutions to ensure that the pathways for water to ingress are properly sealed off. A depth of technical knowledge and experience, along with a proud reputation for integrity and reliability, has made Waterstop Solutions the go-to company for many Defect Managers working for major construction companies across Queensland and New South Wales.
We at Waterstop Solutions have the technical and practical expertise to diagnose the source of the leak and will provide you with our recommended solution to achieving an effective, high-quality, long-lasting repair to stop the water ingress with minimal disruption
We believe in and are committed to always delivering high-quality solutions by utilising the right products and techniques for each specific project combined with our industry-leading know-how on tap. We have a large talent pool of specialist leak sealing and concrete repair technicians with Certificate III in construction waterproofing in Queensland and New South Wales that are extensively trained in our systems and project execution methods.
The leadership positions on every Waterstop Solutions project are operated by highly qualified, certified and experienced industry professionals. Our in-house skills and expertise gained from more than 60 years of industry experience provide a full range of high-quality remedial waterproofing and concrete repair works to commercial buildings, civil infrastructures, industrial sites and residential properties. From waterproofing diagnostics, preventative and remediation solutions – All of our waterproofing solutions are quality guaranteed.