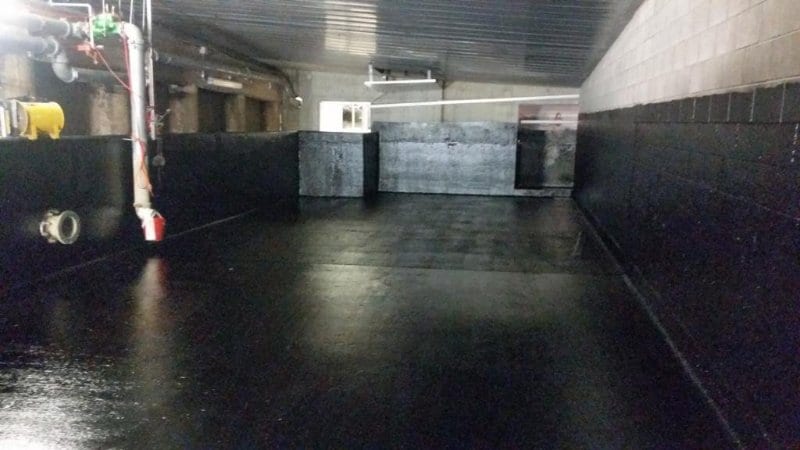
11 May Tricky Leaks in Hospital Fire Water Retention Tanks
Waterstop Solutions was recently commissioned to repair the waterproofing membrane in two leaking fire water retention tanks at a major public hospital in Queensland.
Several repair attempts by other service providers had proven to be futile with recurrent poor membrane adhesion to the substrate in a number of places, which in turn was causing multiple continuous leaks from these two concrete water tanks.
To help protect the patients, staff and property from fire, it is extremely important that the tanks are watertight and a reliable supply of water is available during a fire emergency.
In addition to that, even the smallest defect in the membrane can, over time, lead to costly structural decay, deterioration of building materials and mould growth.
Thankfully, Waterstop Solutions was asked to come up with a solution. Our team thrive on finding solutions through in-house R&D and by networking with our skilful suppliers and other industry professionals.
Tricky waterproofing challenges are what sets us apart in the remedial waterproofing industry – backed by the 50+ years combined experience of Harold Du Toit and Chris Anderson.
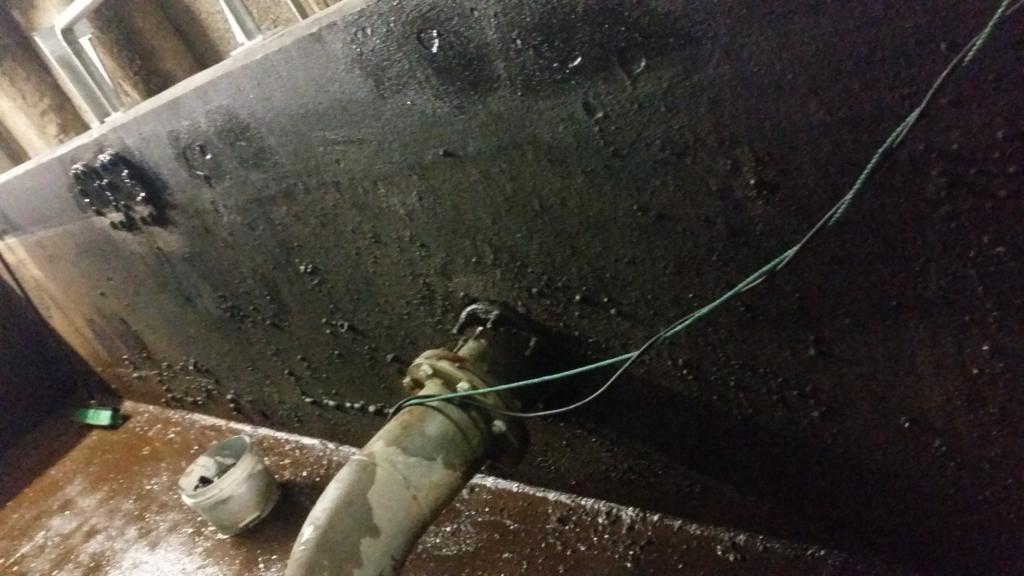
Image: Waterproof membrane in firewater retention tank with failed adhesion causing constant leaks.
We experienced a couple of challenges
Challenge number 1
Identification and mapping of all possible leaks
The tanks were leaking from many places and it was imperative that the remedial waterproofing was 100% watertight.
Prior to Waterstop Solutions being engaged to carry out the remedial waterproofing, a number of repairs to the leaks had been attempted by another contractor, but the problem remained. The recurrent challenges were that the waterproofing membrane did not adhere to the substrate in a number of places, which was causing multiple leaks across the two tanks.
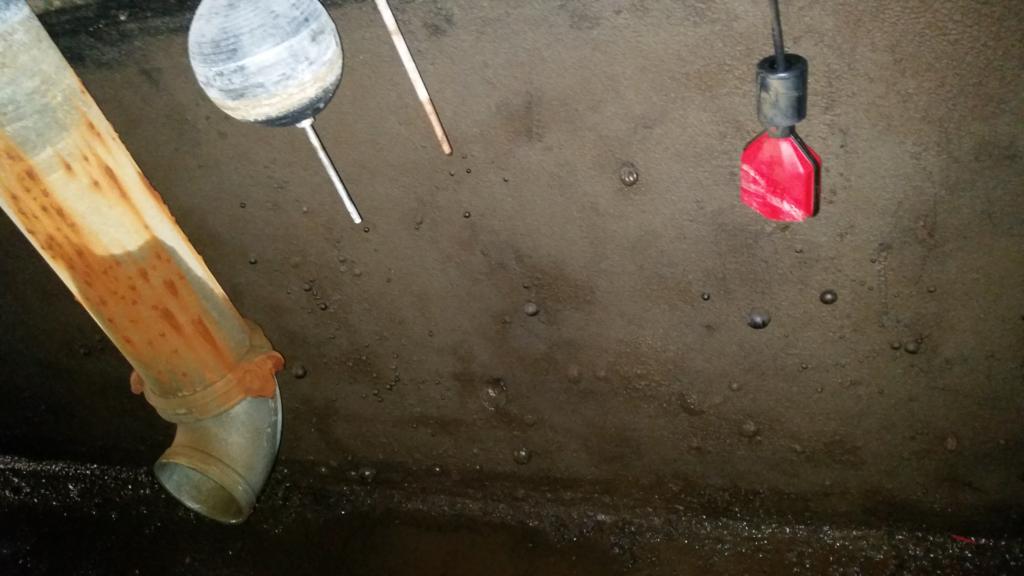
Image: Waterproofing membrane bubbling due to failed adhesion.
To ensure that all possible breaches of the membrane were properly identified, Roberto Scalpelli and his team from International Leak Detection (ILD) Australia were brought in to identify where all the breaches in the membrane were.
At the completion of our waterproofing works, ILD Australia was brought in again to inspect and Re-test the new membrane, using ILD®’s proprietary Electric Field Vector Mapping EFVM® (This method is explained further down in the article). *
Challenge number 2
Downtime, Noise Restrictions and Costs
A full removal of the existing membrane and refurbishment of the water tanks was beyond the bounds of possibility. This approach would have attracted massive costs and a prolonged downtime of empty fire tanks – not to mention the associated risks with that.
There were also noise restrictions to take into consideration around hospital patients and staff.
We partnered up with our suppliers and searched our network to combine our technical skills. We scoured the market for a compatible product that could work with the existing membrane and that would be fully supported by the manufacturer’s full warranty.
Our product supply partners were involved with the testing and checking the quality of our developed application prior to the start of the works. They also supervised quality testing throughout the duration of the works carried out.
The Remedial Waterproofing Solution for the Fire Water Retention tanks
We installed a Specialised Bitumen Modified Highly Flexible Waterproofing Membrane in multiple layers to a moisture barrier primer system. The primer system assists in preventing bubbling or blistering, which is highly likely in remedial waterproofing applications if not performed.
Thorough surface preparation and vigilant detailing of all penetrations and junctions was completed, which is key to successful remedial waterproofing.
The waterproofing membrane systems we use create an effective barrier against waterborne salts. They are also resistant to atmospheric gases and comply to potable water safety standards.
The systems are supported by manufacturer’s warranty for 10 years, which is extendable to a further 10 years with a maintenance application.
The following images show during works and completed remedial waterproofing works by Waterstop Solutions
These two concrete tanks collect stormwater and are part of the main supply of water for the fire sprinkling system throughout the hospital, with a capacity to hold 354,000 litres.
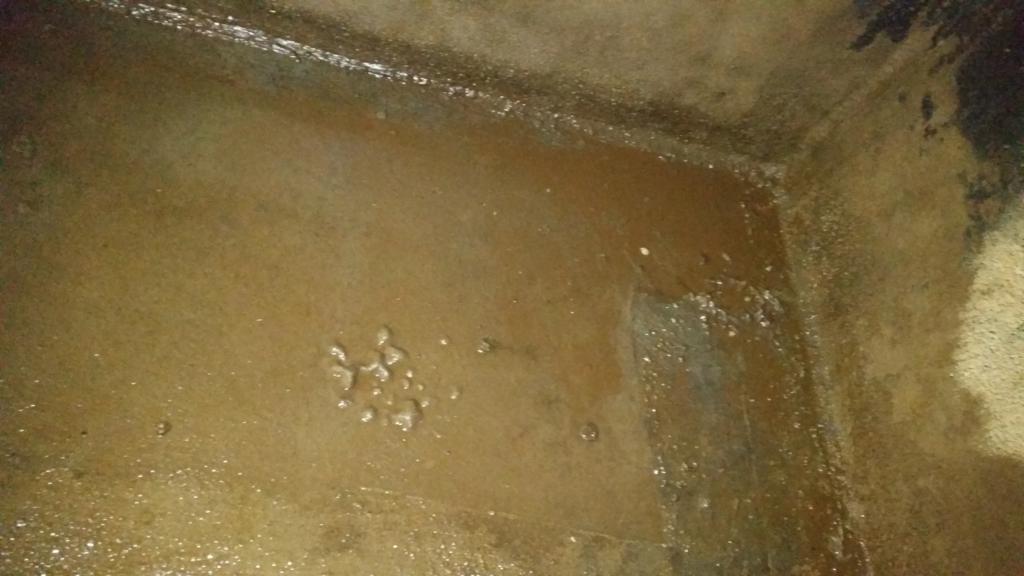
Image: Membrane bubbling due to failed adhesion.
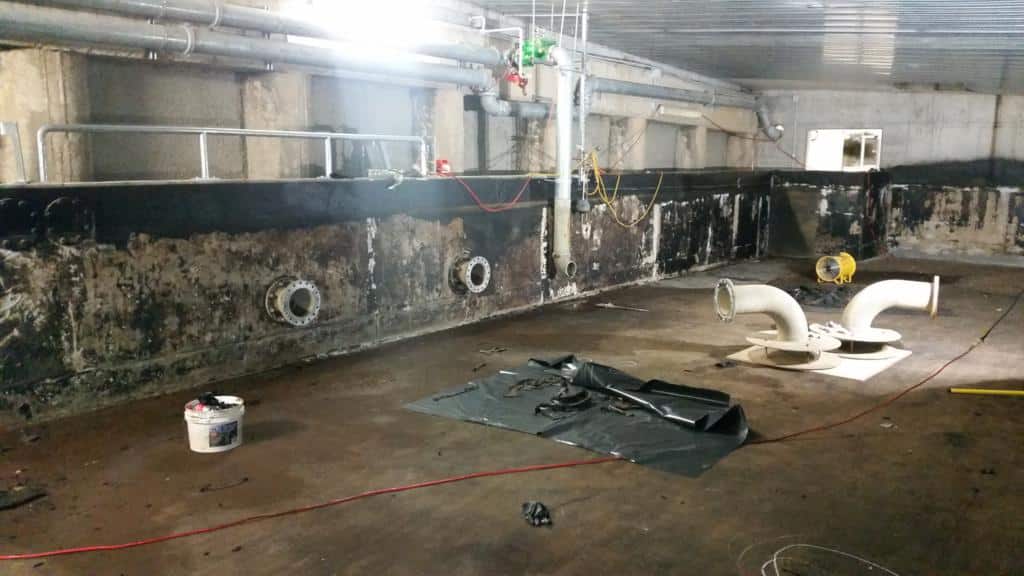
Image: Removal of existing waterproofing membrane. Surface preparation.
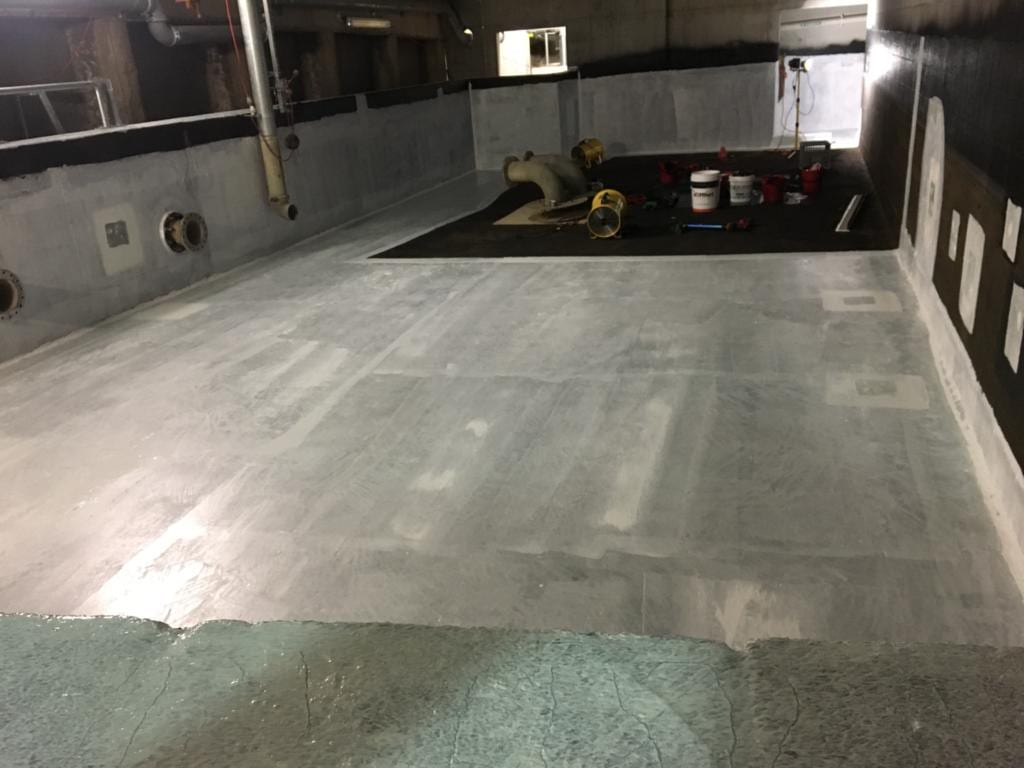
Image: Priming and surface preparation ensuring a full adhesion of the new waterproofing membrane.

Image: Priming and surface preparation ensuring a full adhesion of the new waterproofing membrane.
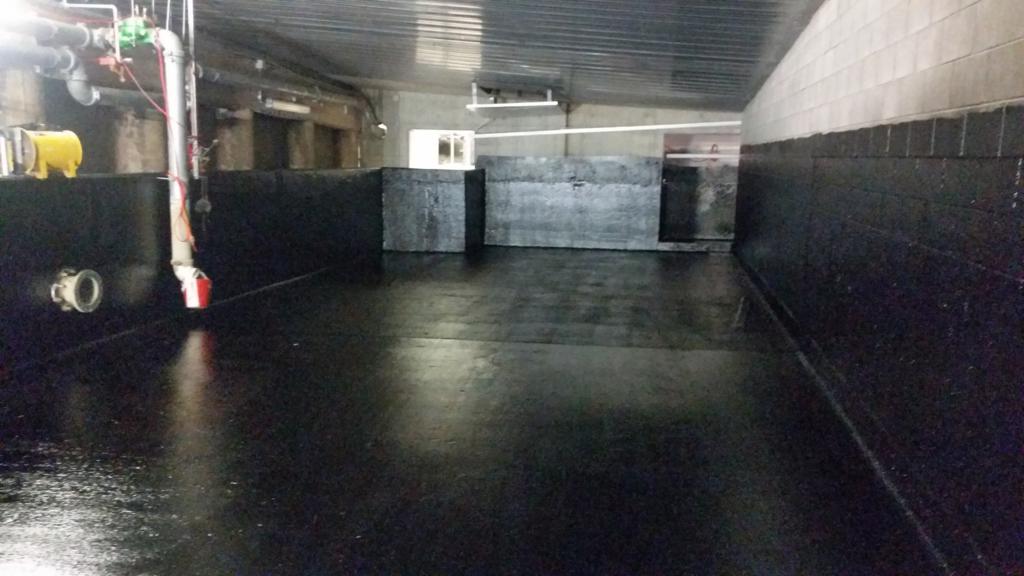
Image: Completed Remedial Waterproofing works of new installation of waterproofing membrane in a QLD public hospital’s Fire Water Retention Tanks.
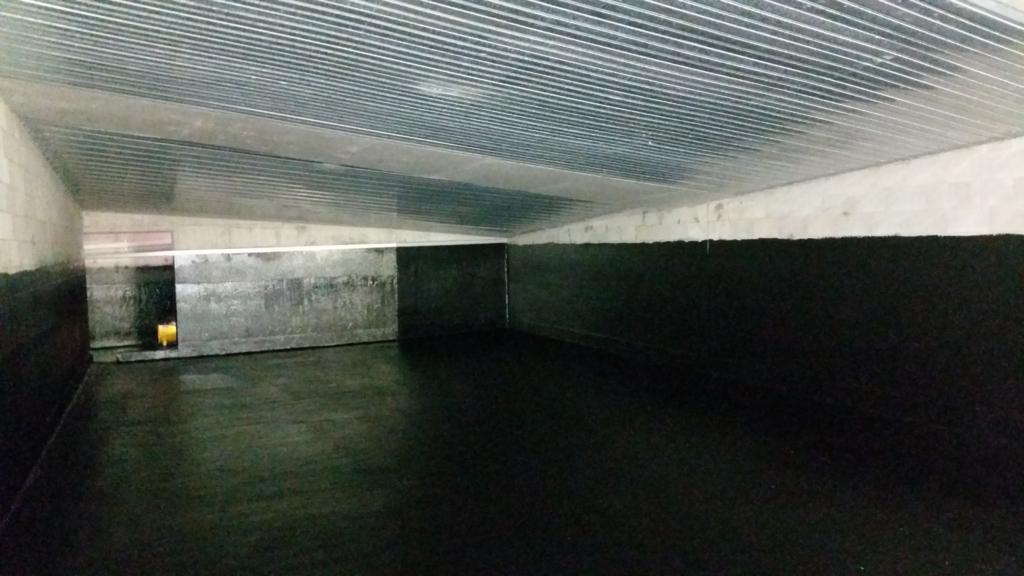
Image: Completed Remedial Waterproofing works of new installation of waterproofing membrane in a QLD public hospital’s Fire Water Retention Tanks.
Quality Control Success
To make certain that no leak went untreated, International Leak Detection (ILD) Australia was requested to carry out a full re-test of the two Fire Service Tanks after Waterstop Solutions’ remedial waterproofing works were completed, in order to confirm the integrity of the waterproofing membrane and that all areas of the tanks were successfully waterproofed, and watertight.
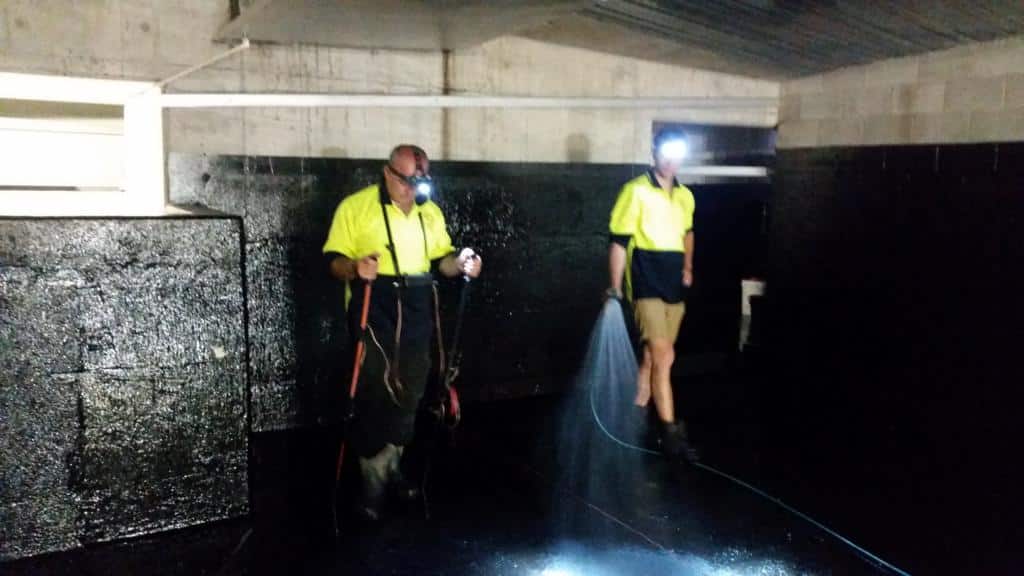
Image: Image shows International Leak Detection (ILD) Australia re-testing the completed remedial waterproofing works by Waterstop Solution
To perform the EFVM® test, the Vector conductor wire was placed on top of the membrane surface and was dampened to create the conductive field plate. As the test progressed, satisfactory readings were observed.
The EFVM® test concluded that the membrane was not isolating the potential difference at (0) locations. Moisture has not penetrated through the membrane at any point the tanks were found to be watertight.
* Water testing with EFVM® Technique
An electrical potential difference is set up between a non-conductive membrane surface, which is wet or thoroughly dampened, and a conductive structural deck or substrate which is earthed or grounded. If there are any leaks, then a small electric current will flow across the membrane surface and down through the puncture to the earthed structural deck.
The electric current will flow directly to the puncture or breach. Using ILD®’s proprietary Electric Field Vector Mapping EFVM®, the direction of the current can be identified and thus a puncture can be pinpointed.
Because of the high electrical resistance through the membrane, the magnitude of the electric current is relatively small. However, the magnitude of the current is not important. Rather, the direction in which the current flows is what leads ILD®’s fully factory-trained inspector directly to the puncture.
A Vector conductor wire is set out in an angular loop around the perimeter of the area to be tested. The ILD® pulse generator is connected to the conductor wire, which delivers a voltage potential, to a predetermined cycle. The ILD® certified inspector, steps into the membrane surface field to be tested, with the EFVM® test equipment and reads the electric flow. If there is any puncture, the EFVM® test equipment will indicate the direction of the current flow, leading the certified inspector directly to the leakage point.
If you have any issues with water ingress, cracking concrete slabs, structural cracks, concrete deterioration, moisture, seepage, efflorescence, rising damp and/or high-flow active leaks in concrete structures, we would be happy to assist you. You are welcome to contact us with any questions that you may have.
We are happy to arrange a site visit with our experienced inspector for an assessment, our recommendations and quotation to carry out remedial repairs.
Follow this link to Book inspection with our senior waterproofer and concrete expert
Brisbane office: (07) 3205 1899
Email: [email protected]
Sydney office: 02 9346 8308
Email: [email protected]
View our Capability Statementand Technical Systems Information Sheet to find out what other services we can provide you with.
Good maintenance begins with a proactive approach to maintain, keep, preserve and protect a building.
Remember that seepage/water ingress into areas such as balconies, basements, concrete roofs, water retention tanks, dams, car parks and retaining walls, should not be ignored – call a remedial waterproofing professional today for an assessment of building defects to provide you with the best solution for your situation.
At Waterstop Solutions, we carry out a wide range of remedial works to concrete structures post-construction stage in Brisbane, Gold Coast, Sunshine Coast, Sydney and outlying areas in Queensland and New South Wales.
Equipped with major civil works experience, we can quickly determine the best approach to rectify all seepage and concrete deterioration issues.
Waterstop Solutions is committed to providing a high standard of service. Our goal is to provide innovative, flexible and practical solutions to ensure the best possible outcomes for our clients. With more than 60 years of combined industry experience in our management team, we lead our workforce with our goal being to deliver exceptional service to build and maintain long-term relationships with our customers.
The best measure of our success is the “follow on” works from our existing clients.
At Waterstop Solutions, we are focused on being the best at what we do – specialised remedial contractors. We do not aspire to become a “one-stop-shop” for trades, which we believe would divert our focus too far from the quality of our remedial work: we do not render, perform carpentry, plumb, paint or plaster. However, we do hold a QBCC Open Builder Licence and often work closely with other such trades. Where only a couple of other trades are required on a job, we offer to subcontract and manage these trades to give our client a complete process when requested. Where more trades are required, we normally refer our clients to a builder who can more closely manage all the work.
Tiling is the only trade which is the exception to the rule at Waterstop Solutions. Since our work often involves disturbing or removing whole sections of tiles, we regularly include the re-laying of tiles in the scope of our work. We are also happy to recommend other reputable tradespeople to our customers, who will ably assist them to complete their projects.