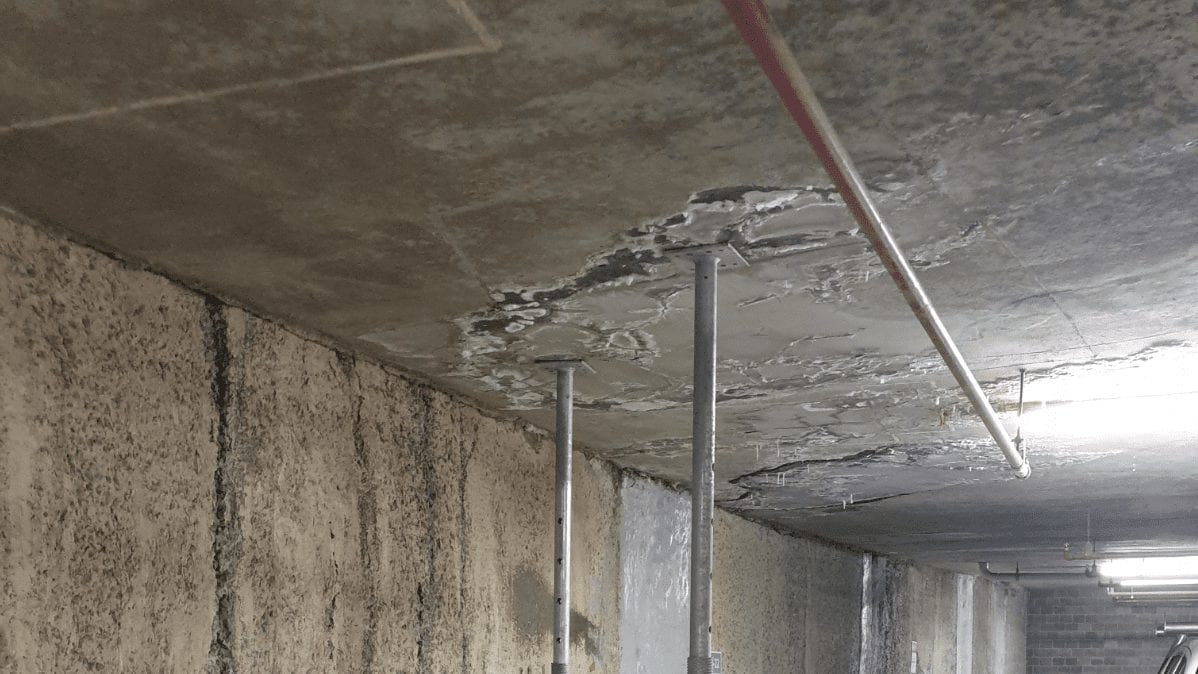
05 Sep Concrete cancer repair – Multilevel underground car park
Environmental stresses on concrete in coastal areas
Reinforced concrete structures degrade with time and exposure to the environment, particularly if that environment contains salts. Reduction of the concrete’s alkalinity either by carbonation or by the ingress of chlorides (salts) are the most common causes of concrete corrosion.
A coastal climate with high humidity, salinity in the soil, salts in rainfall and a high level of airborne salts can accelerate the deterioration of concrete structures. High salinity levels can impact the durability of some building materials, such as concrete and masonry. They are susceptible to accelerated deterioration, such as cracking and spalling, caused by the higher salt concentration and humidity in the environment.
Concrete spalling, or so-called concrete cancer, is quite common in the Gold Coast region and affects many steel-reinforced concrete structures. More so in the older steel-reinforced concrete buildings built 40+ years ago. (Read on for further information about the three conditions that must exist for reinforcing steel to corrode.)
With an excellent preventative maintenance program that protects the concrete structures from premature deterioration from the beginning of a building’s life cycle, a parking garage can last 50 to 70 years or more.
Corrosion of reinforced concrete
When concrete is reinforced with the tensile strength that reinforcing steel rods provide, the composite material resists compression, bending, and other tensile actions.
The high pH (alkalinity) of concrete forms a passive film on the surface of the embedded reinforcing steel rods and acts as a protective shield that prevents or minimises corrosion. Reduction of the concrete’s pH by carbonation or the ingress of chlorides (salt), which are the most common causes of concrete corrosion, causes the steel’s passive film to degrade. Rust begins to form on the unprotected reinforcing steel.
The build-up of corrosion causes tensile stresses as it grows in thickness. The pressure causes the concrete to form cracks near the steel that will, with time, lead to more extensive cracking as the rust builds up until the concrete starts to break away from the reinforcing steel bars (spalling of concrete) and expose the corroded reinforcing steel rods.
Corrosion cycle of steel reinforcement in concrete
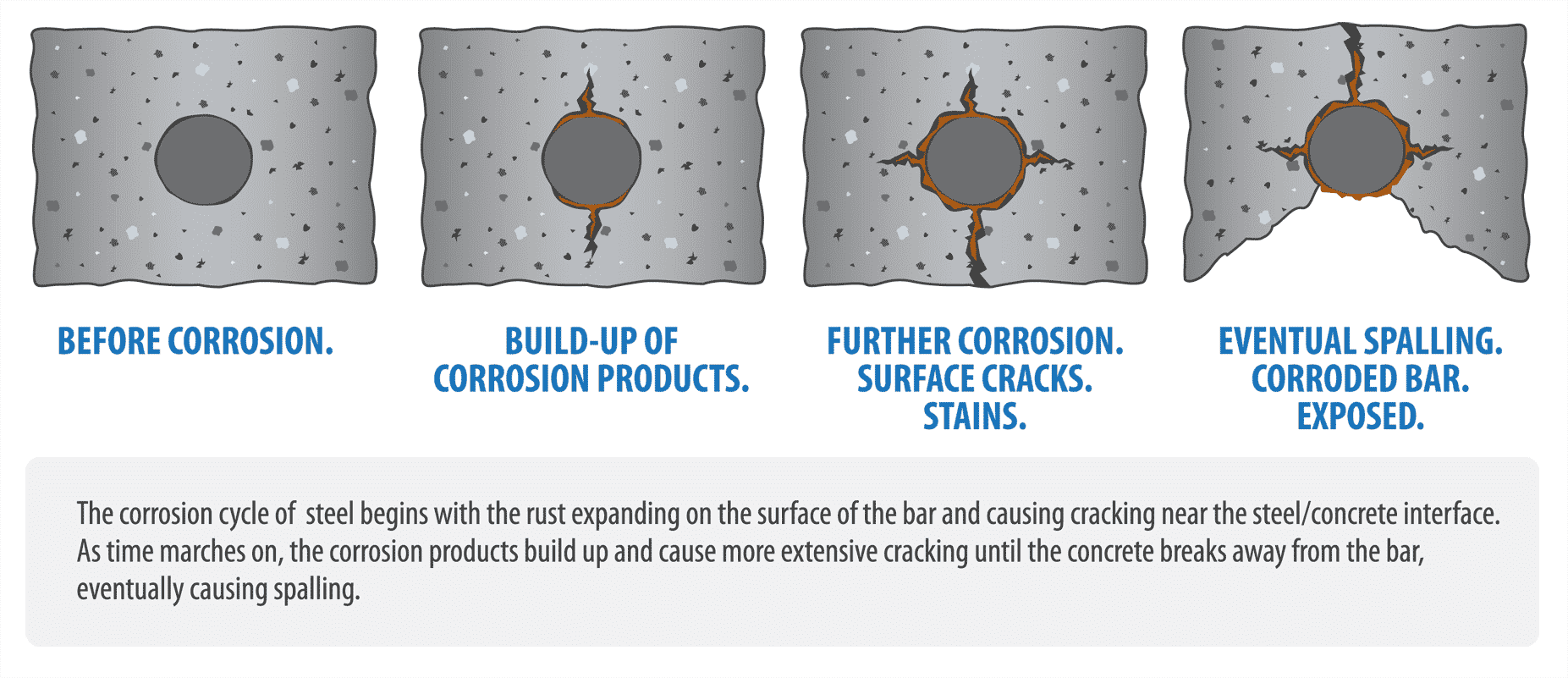
Three conditions must exist for reinforcing steel to corrode:
- The passivation of the steel must have been destroyed by chlorides or by carbonation
- The presence of moisture as an electrolyte
- The presence of oxygen
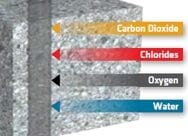
Chloride ions
Exposure of reinforced concrete to chloride ions (salts in air and water) is the primary cause of premature corrosion of steel reinforcement. The intrusion of chloride ions, present in airborne salts and seawater, into reinforced concrete can cause the steel to rust if oxygen and moisture are also available to sustain the reaction. Chlorides dissolved in water can permeate through sound concrete or reach the steel through cracks. The concrete’s alkaline protection to the steel breaks down, promoting corrosion.
Chloride-containing admixtures may also cause corrosion.
Carbonation
Carbonation is a slow-acting process that can result in rusting reinforcement. Carbonation occurs when carbon dioxide from the air penetrates the concrete and reacts with hydroxides, such as calcium hydroxide, to form calcium carbonates in the presence of water. The reduced pH value starts breaking down the passivation film of concrete, which leads to corrosion of the reinforcing steel.
Carbonation-induced corrosion often occurs on areas of building facades that are exposed to rainfall, shaded from sunlight, and have a low concrete cover over the reinforcing steel.
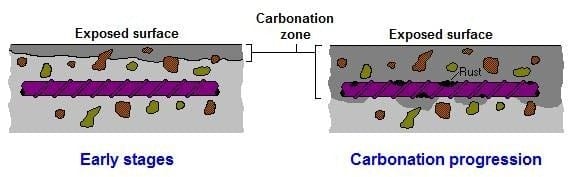
Read More:
Why is anti-carbonation protection of concrete important?
What is the impact of corrosion of reinforcement steel in concrete structures?
Corrosion of reinforcing steel and other embedded metals is by far the leading cause of premature ageing, deterioration and durability issues in concrete.
The passive oxide layer on the steel must fail for reinforcing steel to corrode. If the concrete cover that protects the reinforcing steel is damaged and the bond between the concrete and steel reinforcement bar is broken, the steel’s passive layer will break down, and active corrosion of the steel will start.
When steel corrodes, the resulting rust occupies a greater volume than the steel. The corroding steel reinforcing bars can expand to eight (8) times the volume of the original steel. This expansion creates tensile stresses in the concrete, damaging the surrounding concrete and causing cracks, delamination, and spalling.
The corrosion of reinforcement steel leads to reduced resistance of the steel bars, which, depending on severity, may negatively affect the load-bearing capacity and service life of the concrete.
There are two safety concerns to consider if corrosion is present and left untreated for a long time:
- Loose concrete falling onto pedestrians, vehicles and other assets.
- Risk of collapse due to a reduction in load-carrying capacity.
How can corrosion of reinforcement be fixed?
A typical method of concrete repair process:
-
- Break out unsound concrete and expose reinforcing steel until sound concrete is found and clean non-corroded reinforcing steel.
- Saw cut repair zone perimeter to eliminate feather edges.
- Chisel away the concrete around the reinforcing steel. Prepare substrates – including the removal of any corrosion. Reinstate reinforcing steel and/or add more as deemed necessary.
- After completion of material removal, a concrete primer and rust inhibitor are applied to the steel before reinstating with a high build shrinkage compensated repair mortar. Formwork may be erected to close the cavity before installing the repair products.
- We recommend that the treatment of concrete cancer should incorporate a proper weather/waterproofing system as part of a complete solution, or it risks compromising the life of the repair solution as the underlying cause is likely to continue to affect the structure, depending on the situation.
How can corrosion of reinforcement be minimised in new concrete?
- The first defence against reinforcement corrosion is properly compacting the concrete around the reinforcing steel with quality concrete in a thick layer.
- Reinforcing bars and mesh should be located so that there is enough room between the bars to place and compact the concrete.
- Create a strong bond between the concrete and reinforcement. This allows the tensile forces to be transferred to the reinforcement, thus reducing the width of cracking.
- To help achieve a strong bond, the reinforcing steel should be clean and free from flaky rust, dirt and grease.
- Minimise the water-cement ratio, compact and cure the concrete well. The lower the water-to-cement ratio, the lower the permeability of the concrete. Concrete with low permeability is better able to resist the penetration of water.
- To help protect the concrete against corrosion, apply a quality protective coating system to the finished surface to prevent water from entering the concrete and maintain joint seals.
Follow this link to learn how to repair concrete cancer: CONCRETE CANCER REPAIR WORKS – HOW WE DO IT AND OUR RECOMMENDATIONS.
Follow this link to read more about our various protective coatings: PROTECTIVE COATINGS AND SAFETY COATINGS.
Follow this link to read more about JOINT SEALING AND JOINT REPAIR.
Access more information about defects in concrete structures with a click on the button below. This article discusses the seven most common types of concrete cracks, why they occur, their impact, and how to fix them.
7 Types of Concrete Cracks
Image below: 3 of our specialist technicians in the midst of carrying out concrete repair on a reinforced floor slab in a multilevel underground car park. The goal is to protect the concrete and steel structure from environmental stresses, such as moisture ingress, salty environment and chemical damage, thus prolonging the service life of the concrete slab.
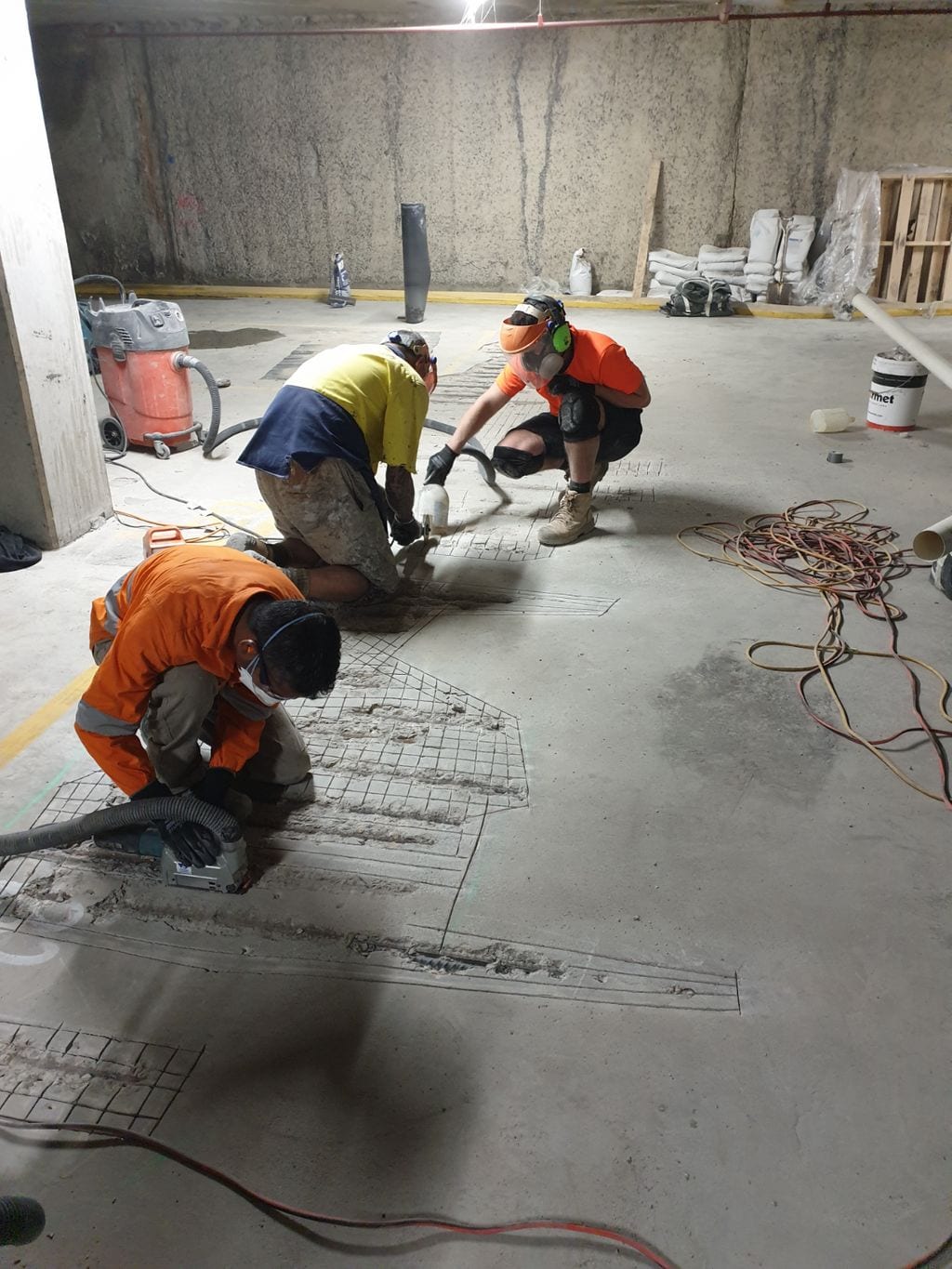
If you have any issues with cracking concrete slabs, structural cracks, concrete deterioration, moisture, seepage, efflorescence, rising damp and/or high-flow active leaks in concrete structures, we would be happy to assist you. You are welcome to contact us with any questions that you may have.
Brisbane office: (07) 3205 1899
Email: [email protected]
Sydney office: 02 9346 8308
Email: [email protected]
Are you interested in learning more about the various remedial building services we provide?
Please click on the image below to download the Waterstop Solutions Capability Statement.
Waterstop Solutions Capability Statement is now available to download as a PDF. (The image is clickable and opens a link to our Capability Statement).
Good maintenance begins with a proactive approach to maintaining, preserving, and protecting a building.
Remember that seepage/water ingress into areas such as balconies, basements, concrete roofs, car parks, and retaining walls should not be ignored – call a remedial waterproofing professional today for an assessment to provide the best solution for your situation.
At Waterstop Solutions, we carry out a wide range of remedial works to concrete structures post-construction stage in Brisbane, Gold Coast, Sunshine Coast, Sydney and outlying areas in Queensland and New South Wales.
Equipped with major civil works experience, we can quickly determine the best approach to rectify all seepage and concrete deterioration issues.